Zero Liquid Discharge Plant
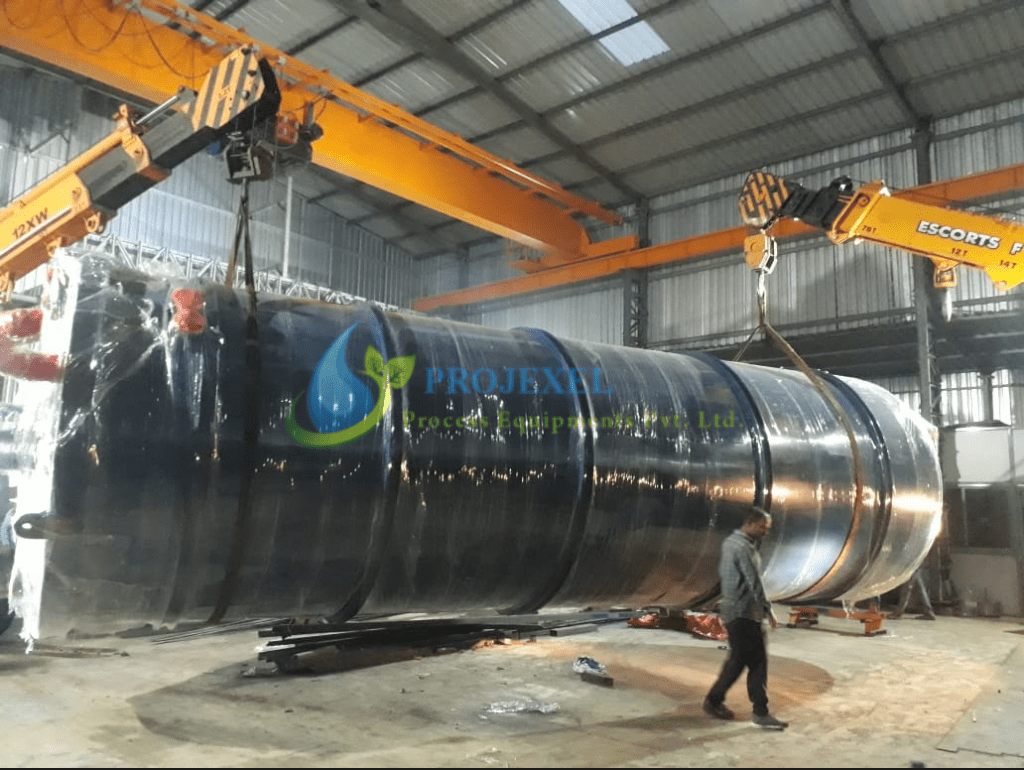
Multiple Effect Evaporator(MEE)
Multiple Effect Evaporator is necessity of all industries which are generating effluent to achieve Zero Liquid Discharge plant. Zero liquid discharge plants is a combination of ETP, RO & Evaporator depending upon nature of effluent. We design the MEE considering the physical and chemical properties of the effluent. Hands on experience in the field ensure the solution at optimum cost of investment and
operation.
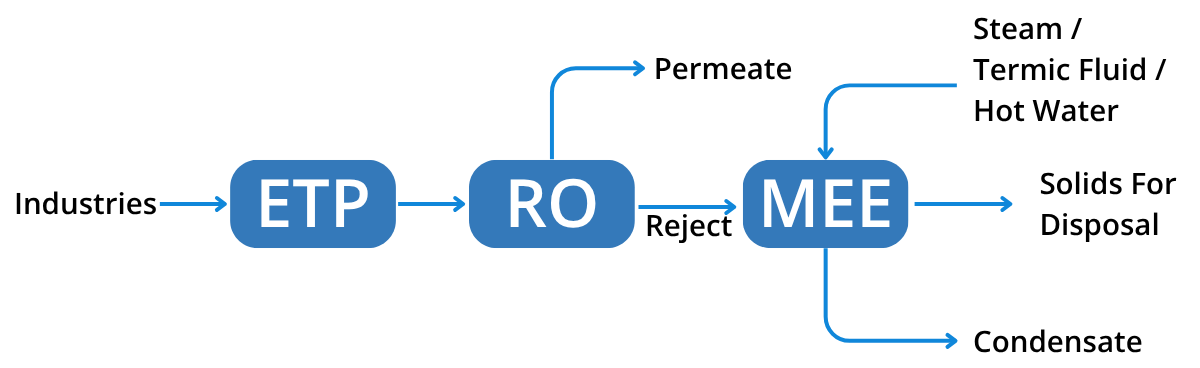
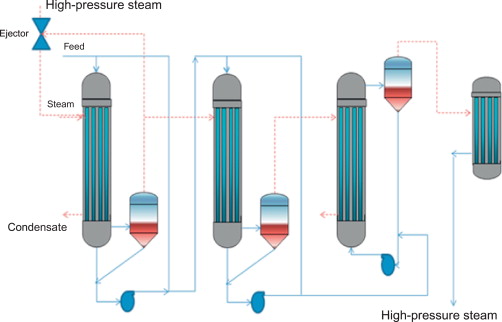
EVAPORATOR BASED ON THERMO VAPOUR RECOMPRESSOR (TVR) TECHNOLOGY
In TVR normally vapour generated from first effect getting mix with live steam, this mixed system used as a heating source for 1st effect by this way we arte enhancing the steam economy.
Three Effect with stripper followed by ATFD
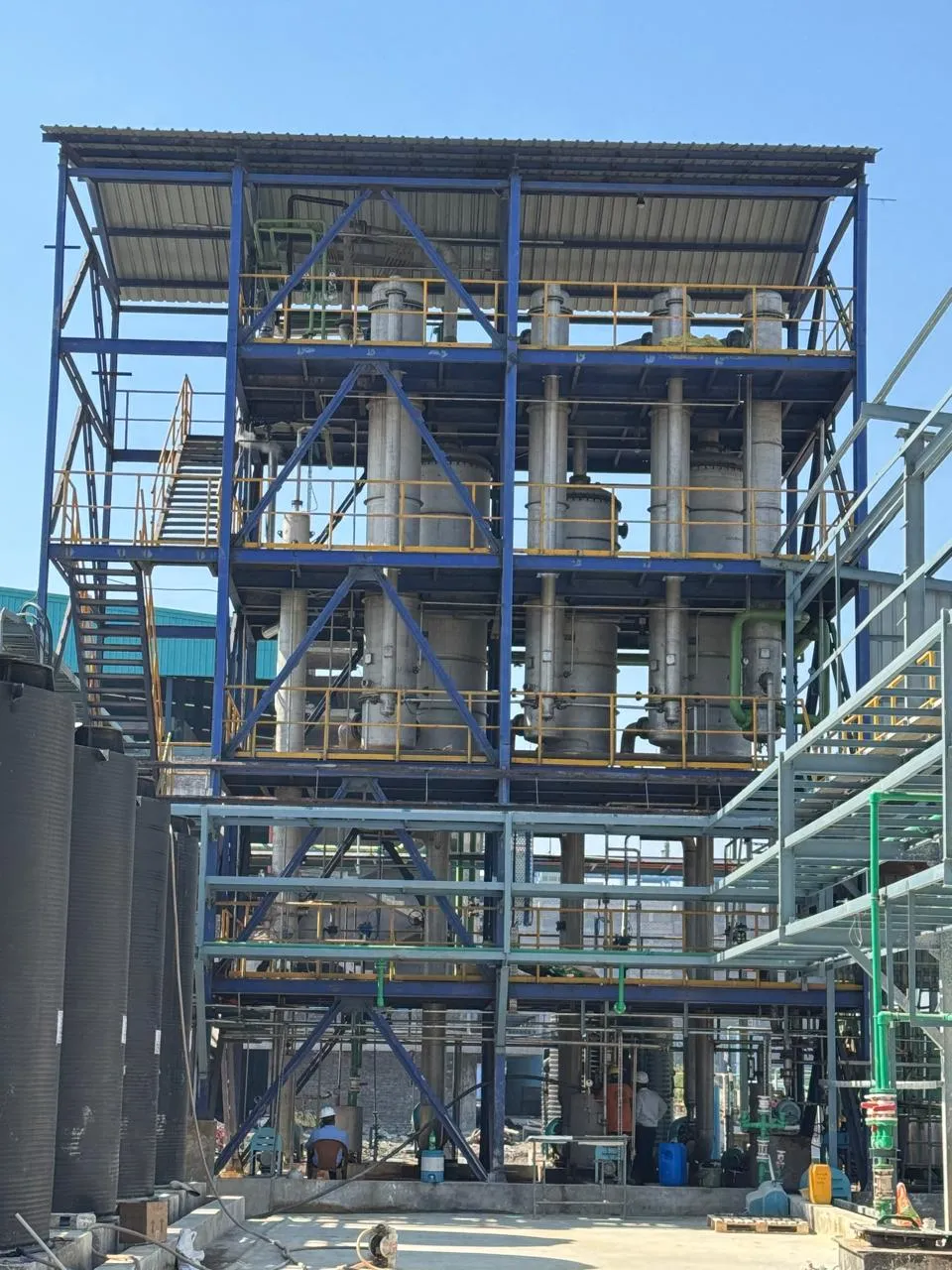
Two effect evaporator followed by Centrifuge
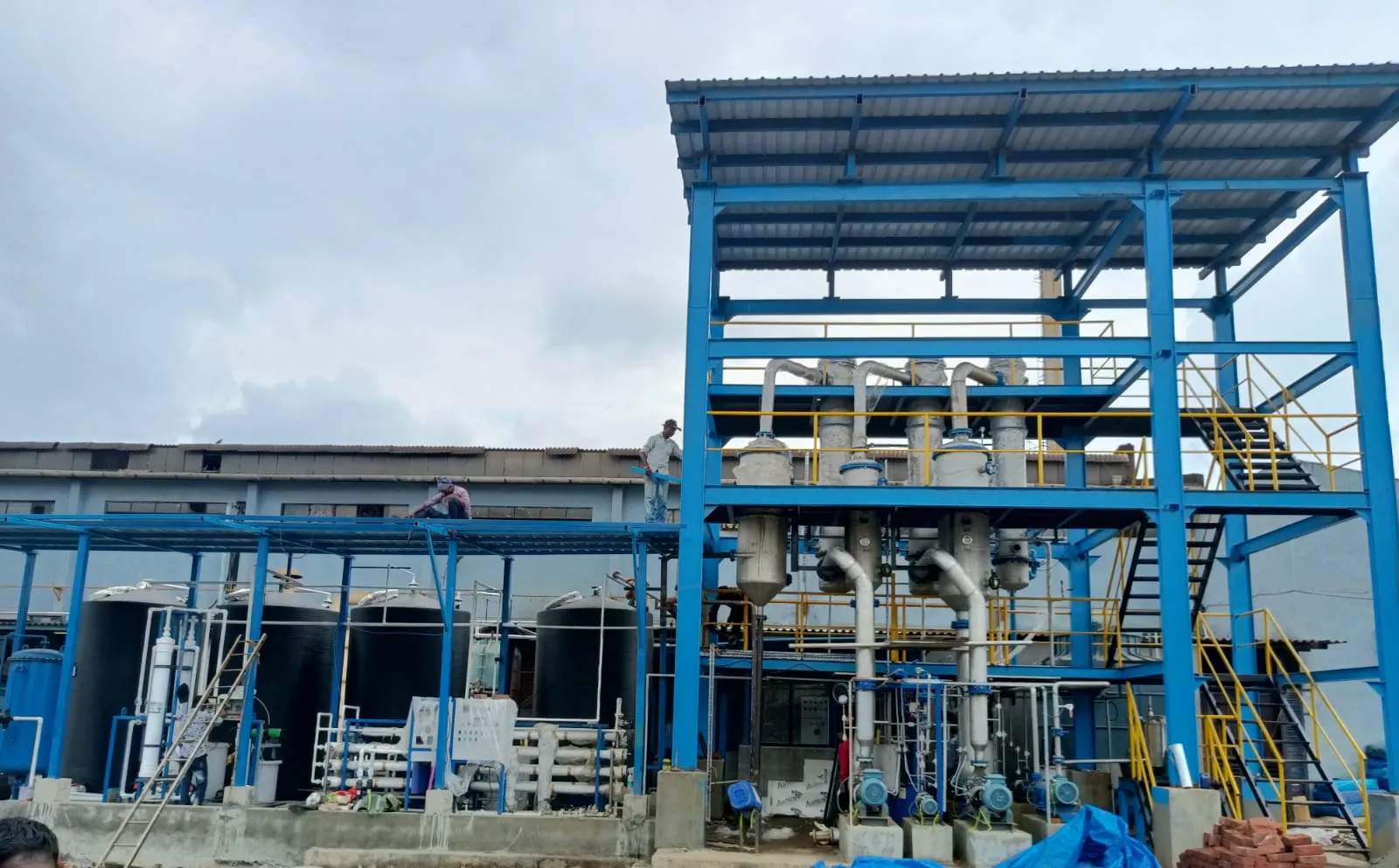
Five Effect Evaporator Followed by Pusher Centrifuge
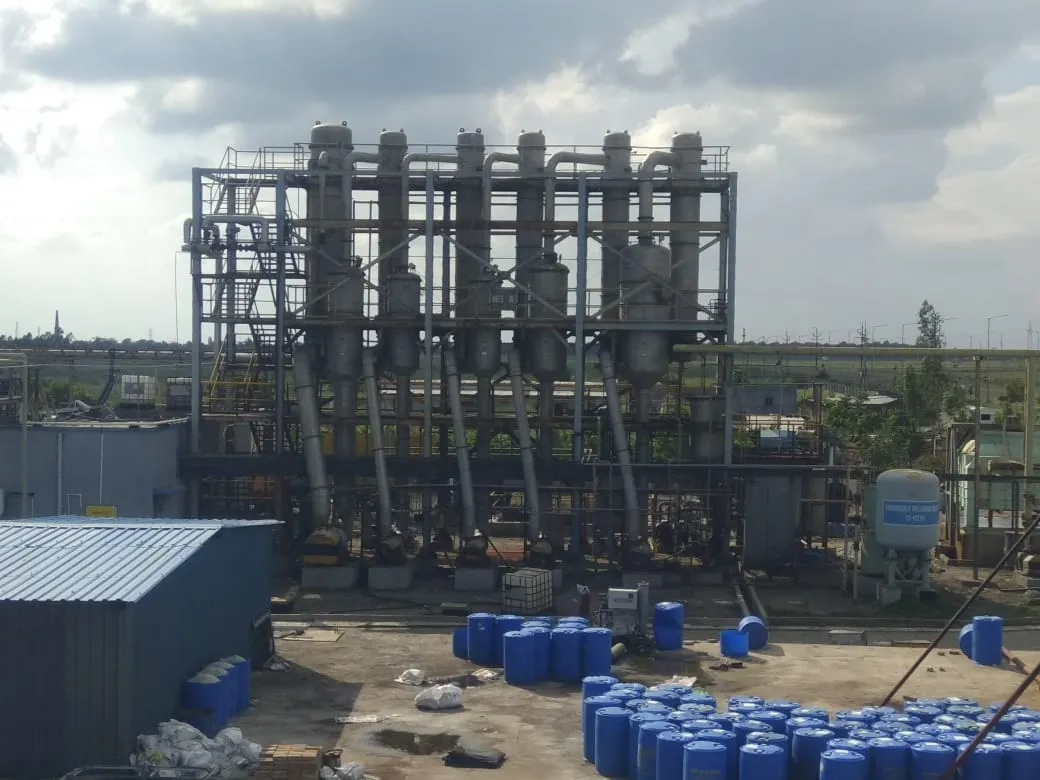
MEE for Molasses and Grain based Distillery
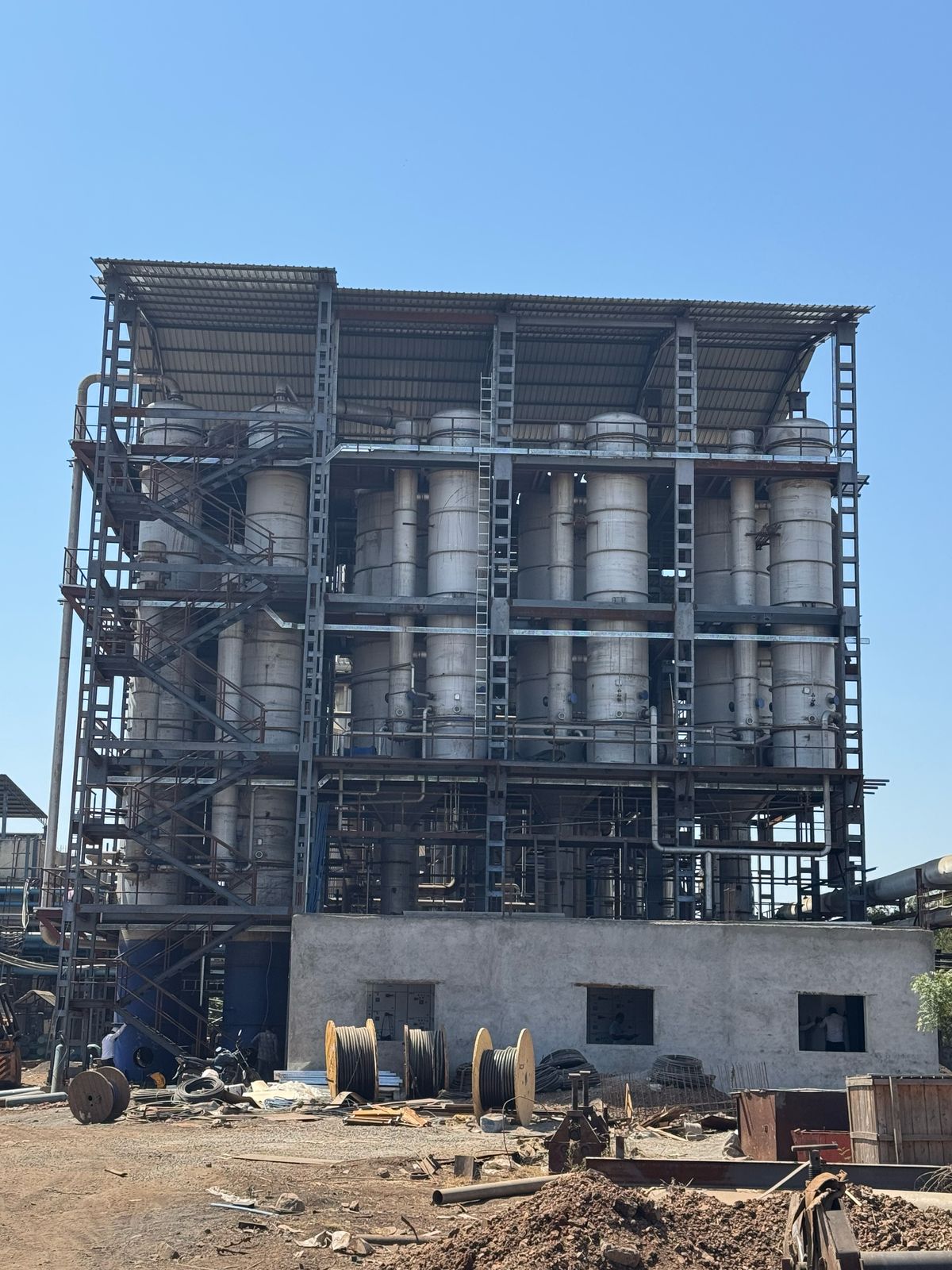
Distillery spent wash has very high BOD, COD and high BOD/COD ratio. The number of inorganic substances such as chlorides, sulphates, phosphates, potassium and calcium are also very high.
We have stipulated stringent norms for proper disposal of spent wash as its uncontrolled discharge may affect the land surfaces and water bodies, particularly the physical, chemical and biological properties of soil and water.
Projexel has Innovative Integrated technology to achieve Zero Liquid Discharge. Integrated evaporation (using alcohol vapours from distillery) offers low energy consumption
The total process condensate water is recyclable after proper treatment and can be recycled back for process, Cooling Tower etc.
The evaporation plants are specially designed to handle molasses raw spent wash, bio-methanated spent wash and grain thin slop to achieve desired solid concentration. Projexel offer evaporation Plants with different combinations of Falling Film and Forced Circulation Multi Effect Evaporation Plant.
The concentrate from the evaporator is further concentrated into the Spray dryer in case of Molasses based distillery or in to the Dryer in case of Grain Based distillery.
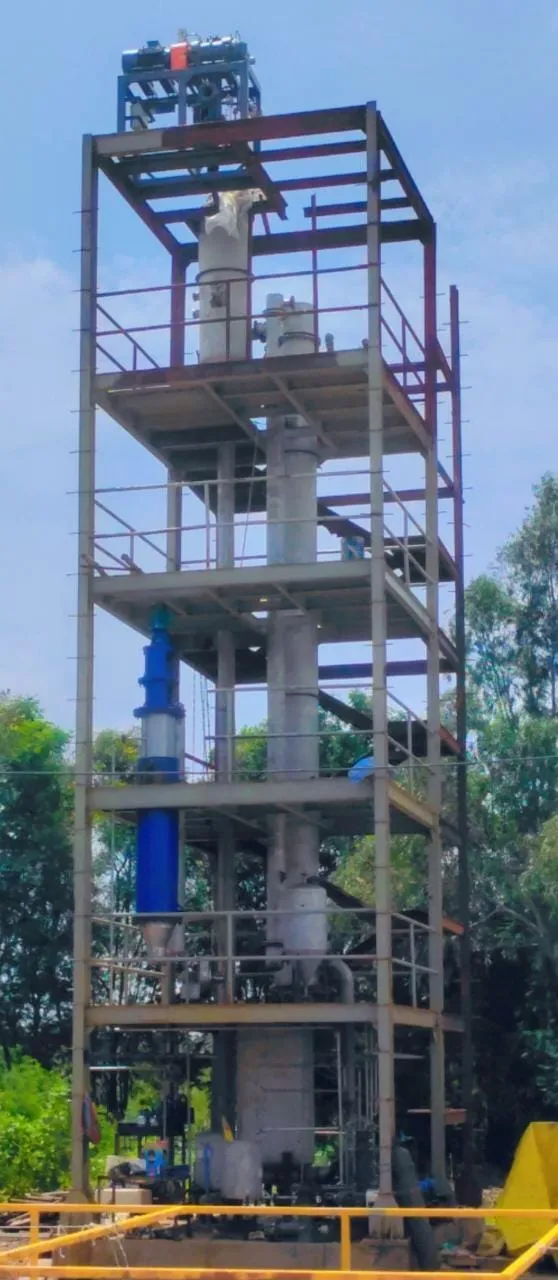
Evaporator Based on Mechnical Vapour Recompressor (MVR) Technology
MVR Evaporator Systems
(Mechanical Vapour Recompression Technology)
Energy-Efficient | Sustainable | Cost-Effective
At Projexel Process Equipments Pvt. Ltd., we specialize in the design and supply of Mechanical Vapour Recompression (MVR) based evaporator systems—an advanced and energy-efficient solution for reducing operating costs and enhancing environmental sustainability in industrial evaporation processes.
Overview of MVR Technology
MVR evaporators typically operate in a single-effect configuration, where all vapor generated is recompressed using a mechanical compressor or blower. This recompressed vapor is then reused as the primary heating medium, significantly reducing the need for fresh steam input.
MVR is the most modern evolution of evaporator technology, following earlier designs like multiple-effect evaporators and thermal vapor compression (TVC) systems. The adoption of MVR technology is driven by the need to:
- Minimize energy consumption
- Reduce fossil fuel usage
- Lower operating costs
- Conserve water
- Support environmental sustainability
How It Works
- Mechanical Vapour Recompression involves:
- Capturing the vapor generated during evaporation
- Compressing it mechanically to a higher pressure and temperature
- Reintroducing it as a heat source back into the evaporator system
Unlike thermal vapor compression, MVR does not require a high volume of live steam, and since no mixing of fluids occurs, nearly all generated vapor is efficiently reused, maximizing energy recovery.
Key Advantages of MVR Evaporators
✅ Significant Energy Savings
✅ Minimal Steam Requirement
✅ Lower Operating Expenses
✅ Reduced Water Losses
✅ High Thermal Efficiency
✅ Environmentally Sustainable
✅ Faster ROI Compared to Conventional Systems
Although MVR systems have a higher initial investment compared to traditional thermal systems, they offer a quick payback due to the drastic reduction in utility costs and long-term operational benefits.
Applications
- Zero Liquid Discharge (ZLD) Systems
- Effluent Treatment Plants (ETP)
- Pharmaceutical & Chemical Processing
- Distilleries & Biofuel Plants
- Food & Beverage Industries
At Projexel, we engineer custom MVR evaporator solutions to meet specific process requirements, offering comprehensive services from design to commissioning. Our systems are built for performance, durability, and long-term energy efficiency.
ATFD (Agitated Thin Film Dryer)
In the ATFD (AGITATED THIN FILM DRYER) the concentrated effluent from the MEE plant is treated for complete separation of solids and liquid.
The selection of ATFD or any other centrifuge depends on the COD value of the effluent.
Many times for small industries having very little effluent generation, it is economical to use ATFD directly (without MEE). The Dry Powder obtained from ATFD can be either used as a by-product or be sent for disposal.
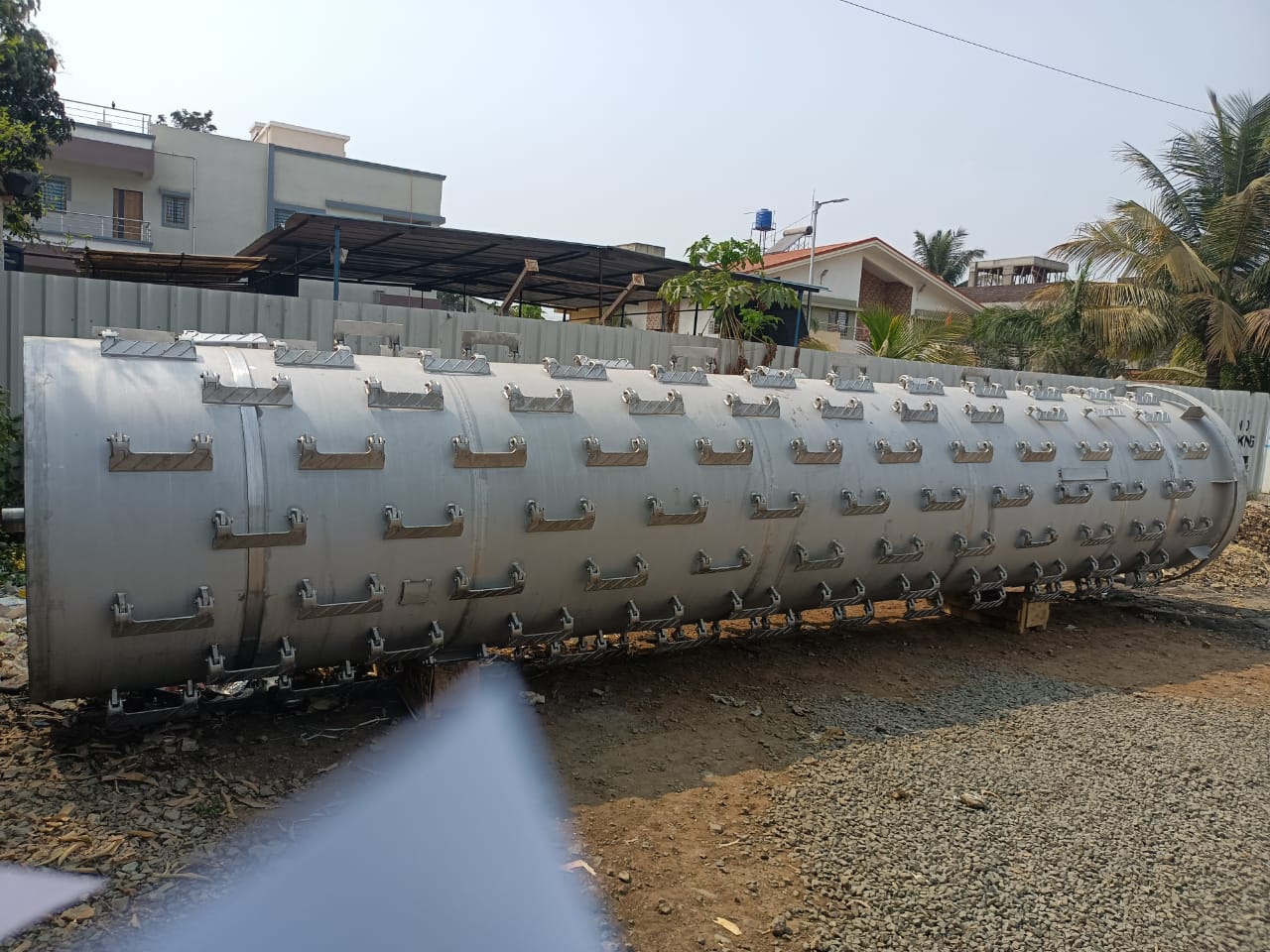
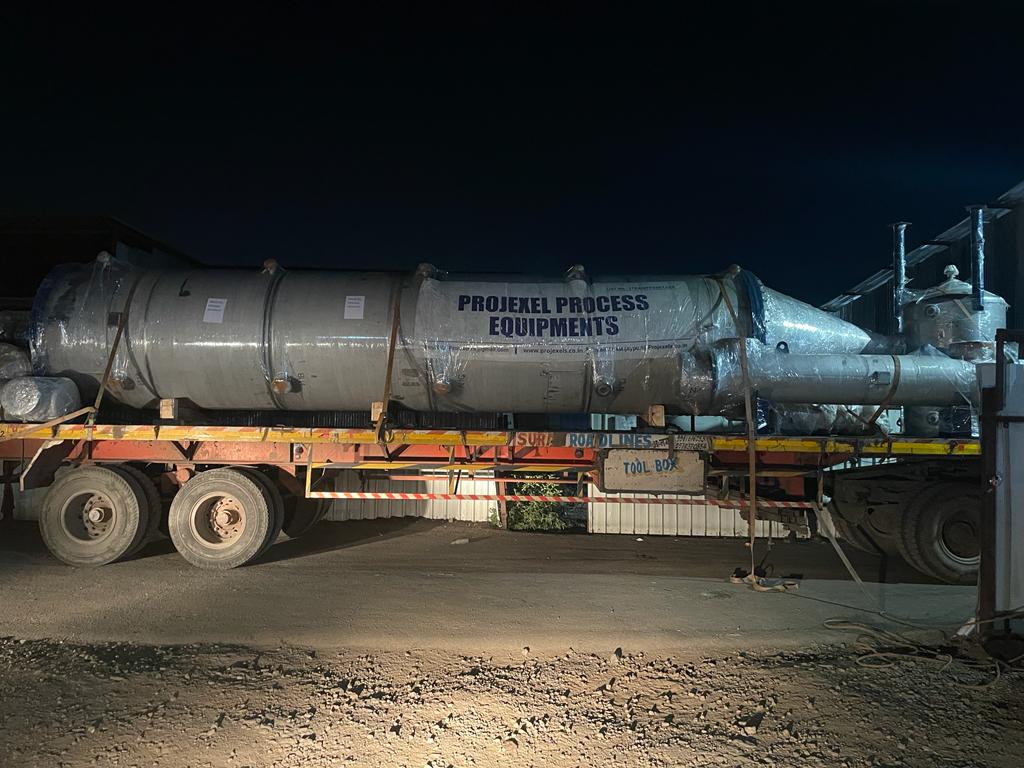
Concept to Commissioning Global Presence R&D-Driven Innovation Trusted by Industry Leaders
The company maintained pace with the desired and planned objectives attempted during its inception, thereby grew very fast.